Are Scheduling Challenges Holding Back Your Manufacturing Efficiency?
Imagine this: a critical order is delayed because key machines sit idle—not due to mechanical failure, but because the right operators weren't scheduled when needed. In the fast-paced and complex world of light industrial manufacturing, such scenarios are costly and all too common. Companies must juggle fluctuating customer demands, a shortage of skilled workers, and strict regulatory compliance—all while striving to reduce costs and boost productivity.
Without effective shift planning software and labor management solutions, these challenges can lead to production delays, increased machine downtime, and overworked employees. This is where workforce scheduling becomes essential. It's not just about filling slots on a timetable; it's the backbone of manufacturing workforce optimization. By ensuring the right workers are in the right place at the right time, you keep operations running smoothly and efficiently.
Optimized employee scheduling directly links your workforce with the tasks that drive your business forward. Leveraging advanced shift planning software boosts productivity and reduces delays. It also balances workloads, enhancing employee satisfaction and retention. When scheduling works well, everything runs smoother—machines hum, orders are fulfilled on time, and your business stays competitive in a demanding market.
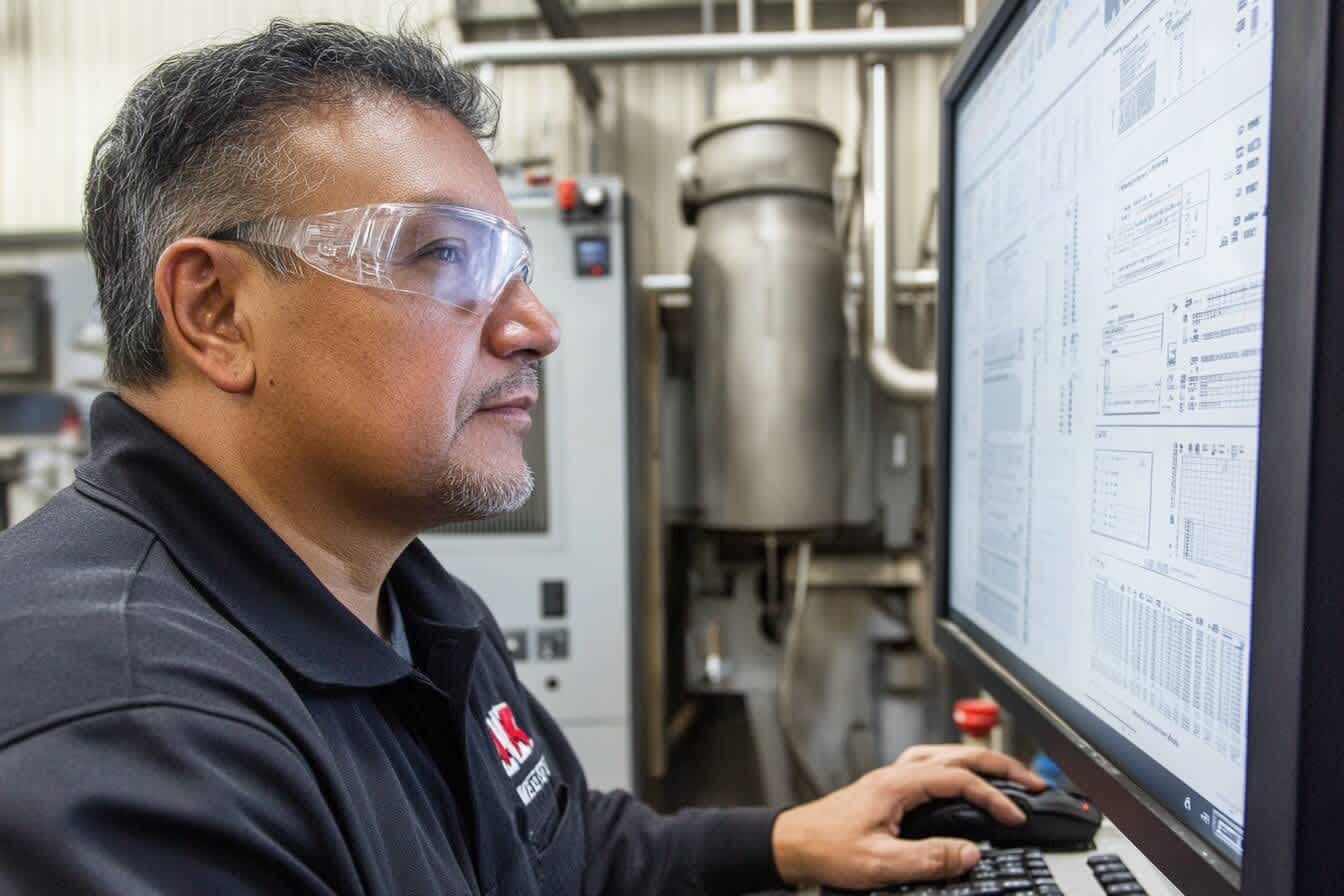
What Makes Scheduling Tough in Manufacturing
In manufacturing, demand often fluctuates due to seasonal trends, market shifts, and unforeseen events. This variability necessitates flexible staffing solutions to align workforce levels with production needs. Traditional fixed schedules may lead to overstaffing during slow periods and understaffing during peak times, both of which can be costly. Implementing dynamic scheduling strategies, such as flexible shifts and cross-training employees, allows manufacturers to adapt to changing demands efficiently. For instance, a study by McKinsey highlights how flexible staffing can significantly improve service levels and reduce idle time in manufacturing settings.
Skilled labor shortages also pose significant challenges, making it difficult to place the right people in the right roles. This gap can lead to decreased productivity, increased errors, and higher operational costs. Research study by Deloitte and The Manufacturing Institute projects that by 2030, the U.S. manufacturing sector could have 2.1 million unfilled jobs due to a lack of skilled workers.
Implementing lean manufacturing principles, such as Kaizen (continuous improvement) and Kanban (workflow visualization), can help mitigate these issues by streamlining processes and making better use of existing personnel. However, without addressing the root causes of the skills gap, these measures alone may not suffice to maintain optimal operations.
Regulatory compliance is essential for keeping operations lawful and efficient. Laws such as the Fair Labor Standards Act (FLSA), which governs minimum wage and overtime, and the Occupational Safety and Health Act (OSHA), ensuring safe workplaces, set clear rules for employers. Ignoring these regulations can lead to hefty fines, lawsuits, and reputational harm, making strict adherence a critical priority for any production facility.
Why Effective Scheduling Makes a Difference
Effective scheduling is the backbone of smooth manufacturing operations. It ensures the right number of workers are present to meet production needs, avoiding costly overstaffing or frustrating understaffing. This balance prevents delays, reduces downtime, and keeps operations running efficiently. Additionally, accurate scheduling helps companies comply with labor laws, reducing the risk of fines or legal issues.
Beyond operational benefits, great scheduling improves employee satisfaction and retention. By accommodating worker preferences and providing clear, consistent schedules, manufacturers can reduce turnover and create a more engaged workforce. Some key advantages of effective scheduling include:
Lower labor costs by reducing overtime and idle time.
Fewer bottlenecks through better alignment of staff with production demands.
Increased flexibility to adapt to last-minute changes in demand or operations.
These benefits highlight why workforce scheduling is more than just a task—it’s a strategic tool for success.
Achieving these benefits can be challenging without the right tools. Manual scheduling is time-consuming, prone to errors, and struggles to adapt to the fast-paced demands of manufacturing. This is where workforce scheduling software like Timewave makes a difference. By automating and optimizing the scheduling process, Timewave ensures your team is always aligned with production needs while reducing costs, improving flexibility, and enhancing employee satisfaction. Let’s take a closer look at how Timewave delivers these results.
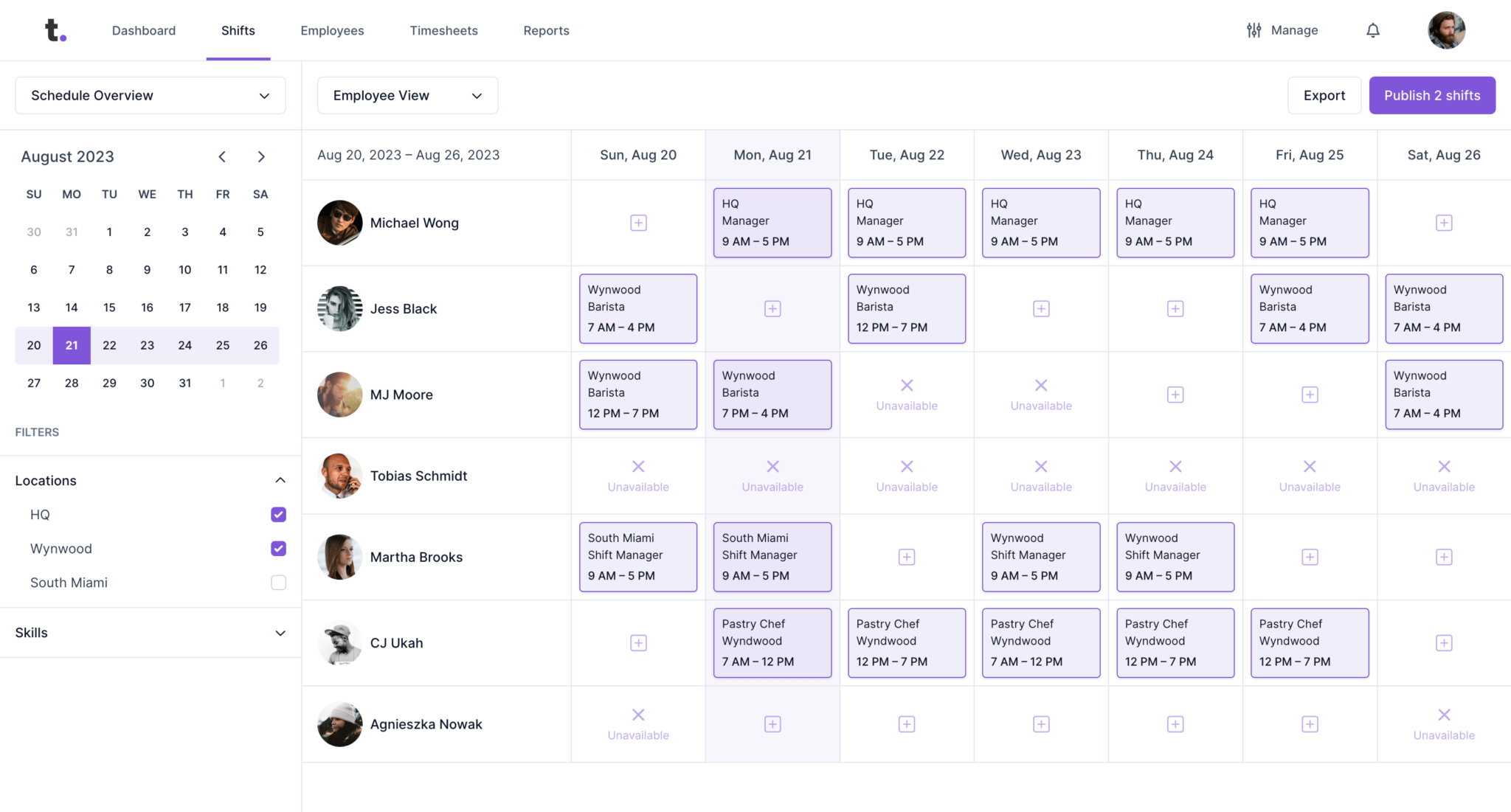
Features That Make Timewave the Best Scheduling Tool for Manufacturers
Timewave is built to address the everyday scheduling challenges manufacturers face. It streamlines the process, making it easier to adjust to changing needs and keep everything on track. From handling last-minute changes to helping employees manage their shifts, we offer features that make scheduling simpler and more effective. Here’s how it works to support your business.
Smart Shift Scheduling
Smart Shift Scheduling ensures that the right employees are scheduled at the right time to meet production demands. Timewave takes into account worker availability, qualifications, and shift preferences to create efficient schedules tailored to your factory’s needs. This reduces the risk of overstaffing during slow periods or understaffing during busy times, helping you maintain smooth production and control labor costs. By automating this process, Timewave saves hours of manual work, so you can focus on managing operations, not spreadsheets.
With Smart Shift Scheduling, you can also adapt to last-minute changes with ease. If a worker calls in sick or production requirements change unexpectedly, Timewave’s system provides suggestions for replacements based on real-time availability and skills. This feature ensures that your production line stays fully staffed and reduces the stress of last-minute disruptions. Whether you’re planning for steady operations or tackling peak demand, Timewave keeps your workforce aligned and ready to perform.
Shift Patterns
Shift Patterns make it simple to plan and manage recurring schedules by allowing you to create predefined shift templates. Whether you need consistent schedules for assembly line workers or rotating shifts to balance workloads, Timewave gives you the flexibility to set up patterns that match your operational needs. You can also customize templates for different departments, machines, or roles, ensuring that every part of your production process is covered without starting from scratch each week.
For manufacturers with complex schedules, the ability to reuse and adjust existing templates saves time and reduces errors. Need to tweak a pattern to account for seasonal demand or add new roles? With Timewave, you can quickly update templates and apply changes across your entire workforce. By standardizing shift planning with templates, you gain consistency, efficiency, and peace of mind knowing your schedules are accurate and reliable.
Productivity Metrics and Analytics
With Productivity Metrics and Analytics, Timewave provides real-time insights into your workforce's performance through intuitive dashboards and custom reports. These tools help you track key metrics like shift coverage, labor costs, and overtime hours, giving you a clear view of how efficiently your schedules align with production demands. Dashboards offer an at-a-glance summary of workforce utilization, while custom reports allow you to dive deeper into specific trends or problem areas. By identifying inefficiencies and bottlenecks, you can make data-driven decisions to optimize scheduling and keep your operations running smoothly.
Intelligent Time and Attendance Tracking
Intelligent Time and Attendance Tracking in Timewave simplifies the process of monitoring workforce hours, ensuring accuracy and efficiency in a manufacturing setting. With tools like mobile and iPad apps, as well as QR code-based clock-ins, employees can easily log their time, even in dynamic factory environments. Managers can review, update, and approve timesheets quickly, reducing administrative workload and ensuring workers are paid accurately.
Timewave also offers smart timesheet importing powered by AI, which allows you to upload and process timesheets in any format your team uses internally. This feature eliminates the hassle of reformatting data or reconciling errors, making it easier to integrate time tracking into your existing workflows. By streamlining time and attendance tracking, Timewave helps manufacturers reduce discrepancies, save time, and maintain reliable records that support labor compliance.
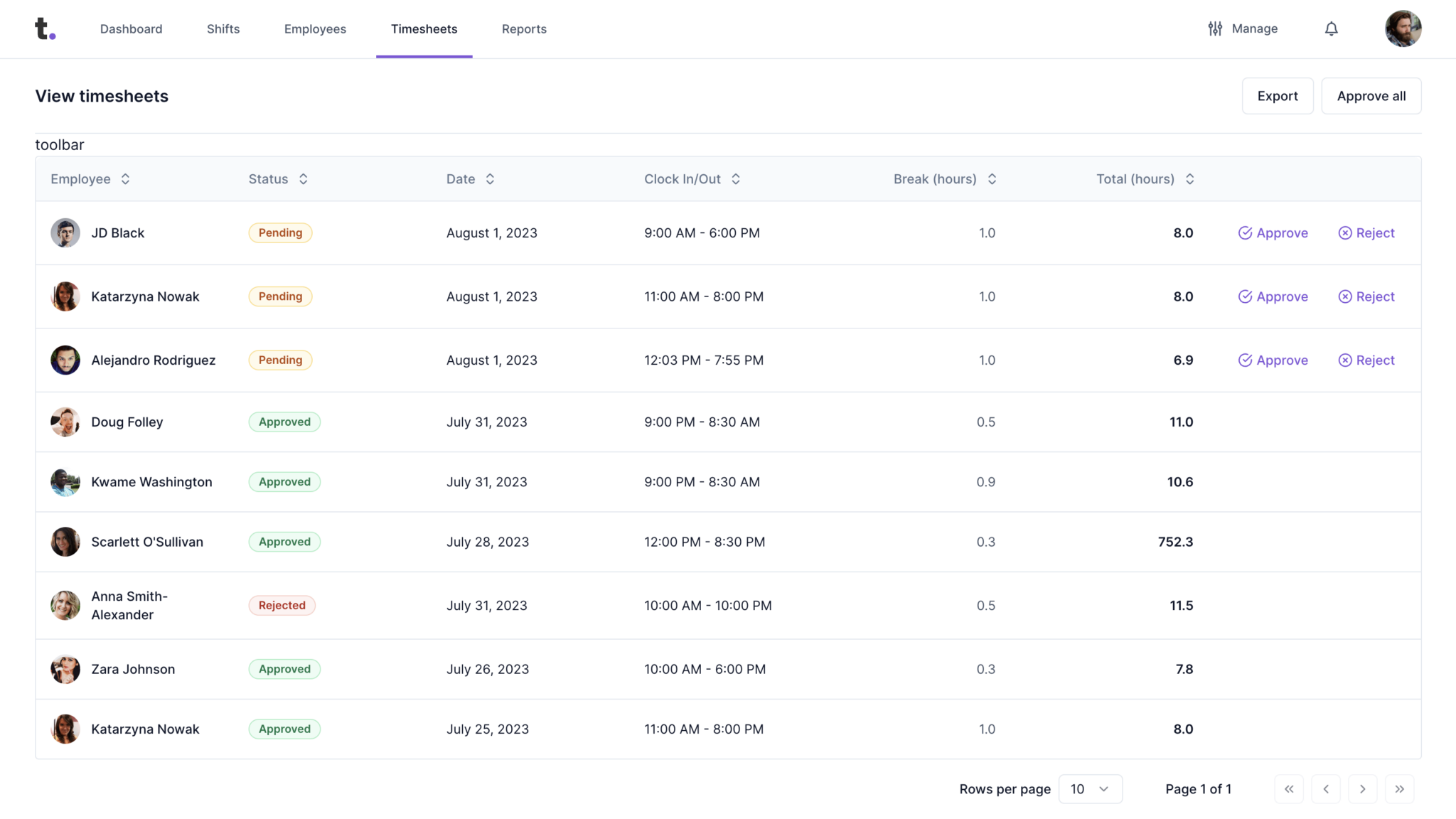
The Future of Workforce Scheduling in Light Industrial Manufacturing
The future of workforce scheduling lies in harnessing advanced technologies to create smarter, more adaptive systems. AI and predictive analytics are revolutionizing how manufacturers forecast labor needs. By analyzing production trends, demand cycles, and historical data, AI-powered tools can predict workforce requirements and align scheduling to meet them. This ensures that manufacturers stay prepared for peak demand while minimizing labor costs during slower periods, improving overall efficiency and productivity.
As manufacturing embraces Industry 4.0, workforce scheduling is becoming an integral part of the connected factory. By integrating scheduling tools with machine monitoring systems, ERP platforms, and other operational technologies, manufacturers can create seamless workflows that respond dynamically to real-time changes. For example, when a machine goes offline or production rates shift, smart scheduling systems can instantly adapt staffing plans to maintain operational balance.
Finally, the focus on employee well-being is becoming a key driver of scheduling innovation. Advanced tools make it easier to accommodate worker preferences, offer flexible shift options, and prevent overwork. By fostering a healthier work-life balance, manufacturers not only improve employee satisfaction but also enhance retention and performance, creating a more engaged and productive workforce. A study by the Manufacturing Institute found that 68% of manufacturing employees cited their job fitting well with other life demands as a key reason for staying with their employer. The future of workforce scheduling isn’t just about efficiency—it’s about building stronger, more resilient teams.
Conclusion
Workforce scheduling is the backbone of operational success in light industrial manufacturing. By effectively aligning labor with production demands, enhancing employee satisfaction, and ensuring regulatory compliance, optimized scheduling keeps your operations running smoothly and efficiently. The right scheduling tools are essential for overcoming industry challenges and maintaining a competitive edge.
Ready to transform your workforce management and boost your productivity? Discover how Timewave’s advanced shift planning and labor management solutions can revolutionize your manufacturing operations. Start your free trial today and experience firsthand how Timewave can streamline your scheduling, reduce costs, and enhance employee satisfaction. Don’t wait—unlock your manufacturing potential with Timewave.